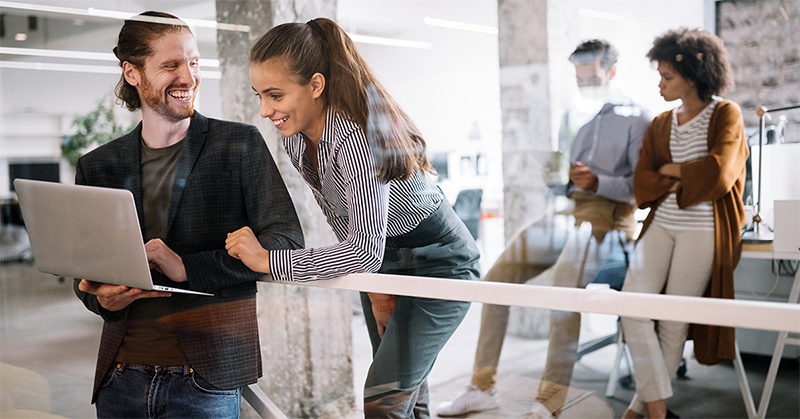
Automation
Process mechanization is a tool that can streamline and optimize workflows, making them more efficient and effective. Despite its many benefits, process automation can be a complex topic to understand. This article will explain process mechanization in simple English and explore some of its key concepts and benefits.
What is Process Mechanization?
Process mechanization uses technology to automate repetitive, time-consuming, and often mundane tasks that humans typically perform. This can include data entry, invoice processing, and customer service inquiries.
To automate a process, a business must first identify the specific tasks that can be automated. This may involve mapping out the steps involved in the process and identifying areas where automation can be introduced. Once the automation has been implemented, the process can be executed automatically without human intervention.
Process mechanization can take many forms, from simple macros and scripts to more advanced tools and software solutions. Process mechanization technologies have significantly increased availability in recent years, including robotic process automation research (RPA), machine learning, and artificial intelligence.
Why Automate?
There are many reasons why businesses might choose to automate their processes. Some of the most common benefits include:
Improved accuracy: Automated processes can reduce errors and ensure that tasks are performed consistently and accurately every time.
Cost savings: By reducing the need for human labor, businesses can save on labor costs and free up resources for other business areas.
Improved customer experience: By automating tasks like customer service inquiries, businesses can respond to customer needs more quickly and efficiently, improving overall customer satisfaction.
Reduced risk: Automated processes can help to mitigate risk by reducing the chance of errors or oversights.
Getting Started with Process Mechanization
If you are considering implementing process mechanization, there are a few steps you can take to get started:
- Identify the process: The first step in implementing process mechanization is identifying the processes you want to automate. It may involve mapping out the steps involved in the process and identifying areas where automation can be introduced.
- Determine the level of automation: Once you have identified the process, you will need to determine the required level of automation. This may involve using simple macros and scripts or more advanced tools and software solutions.
- Evaluate automation technologies: There are many different types of automation technologies available, including robotic process automation, machine learning, and artificial intelligence. You will need to evaluate these technologies to determine which is best suited to your needs.
- Choose a vendor: If you use a third-party vendor to implement your automation, you must choose a vendor with experience in your industry and who can provide the support and services you need.
- Implement and test: Once you have chosen your automation technology and vendor, you must implement the automation and test it thoroughly to ensure it works as expected.
- Monitor and optimize: After the automation has been implemented, monitoring its performance and optimizing it over time is crucial to ensure that it continues to meet your needs.
Summing Up
Automating repetitive tasks allows businesses to free up resources for more high-value tasks and improve the overall customer experience. Suppose you are considering implementing automation in your business. In that case, it is essential to start by identifying the specific processes that can be automated and evaluating the different types of automation technologies that are available. With the right approach and support, process mechanization can be a valuable tool for businesses of all sizes and industries.